Značku BMW si odjakživa podvědomě spojujeme s bavorskou metropolí, ale pro její motocyklovou divizi je Mnichov jen vývojovým a administrativním centrem. To podstatnější – tedy samotná výroba jednostopých vozidel – se už před čtyřiceti lety přestěhovalo do berlínské čtvrti, jejíž český název zní Špandava.
Vztah Bayerische Motoren Werke k hlavnímu městu Německa má však ještě hlubší kořeny. Historicky první motocykl s typickým modrobílým logem – model R 32 – byl světu představen na tamní výstavě v roce 1923. Na začátku druhé světové války pak firma BMW koupila ve Špandavě továrnu na výrobu leteckých motorů a provozovala ji dalších deset let bez zásadních změn v produkci. Ale poválečný vývoj si vyžádal uvolnění výrobní kapacity mnichovských montážních linek pro automobily a výroba motocyklů se postupně přesunula do města rozděleného slavnou zdí. Ze západní části Berlína se motorky vozily nejprve po dílech do mateřské továrny, což muselo být vzhledem k uspořádání tehdejšího Německa poměrně tvrdým logistickým oříškem, a tak byla v roce 1969 zahájena kompletace přímo v berlínských halách z červených cihel.
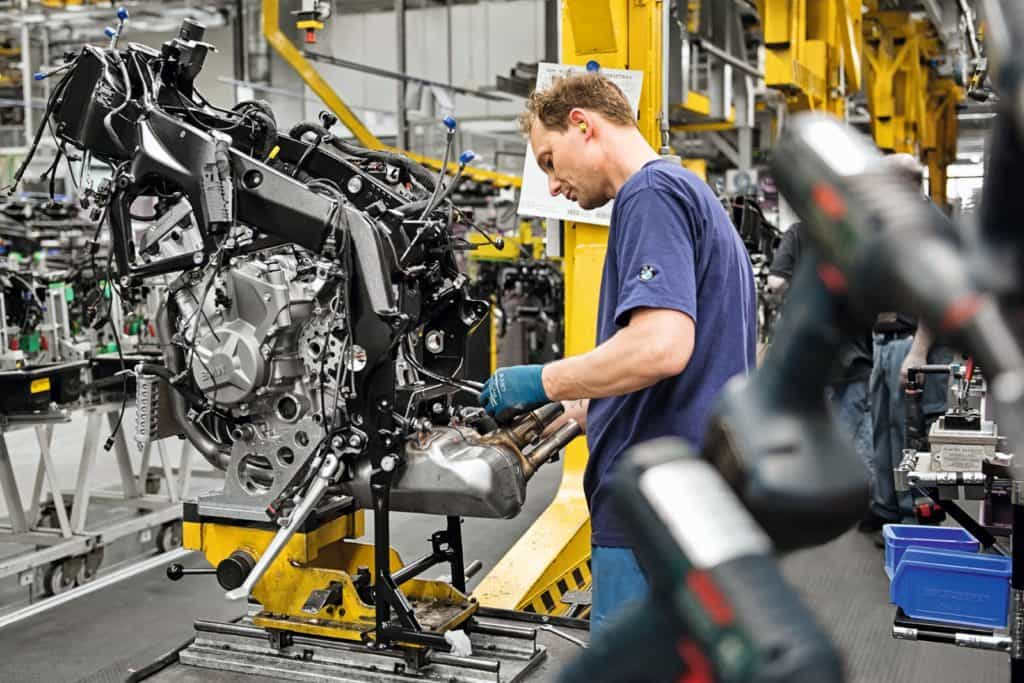
Ty svému účelu slouží dodnes – památkáři jsou přísní všude –, ale v jejich blízkosti vyrostly další, modernější budovy. Denní kapacita totiž narostla z počátečních třiceti kusů, vyráběných rukama čtyř stovek zaměstnanců, na současných 800 motocyklů. Na jejich produkci se podílí téměř dva tisíce techniků, kterým pomáhá armáda robotů. Kromě všech 25 motocyklových modelů z aktuální nabídky BMW se v berlínském komplexu vyrábí ještě brzdové kotouče pro automobily, ale ty tvoří jen okrajový sortiment. Převážná část areálu o rozloze třiceti fotbalových hřišť patří výrobě motorek a takzvaných CKD kitů, což jsou v překladu sady komponentů, určené k finální montáži v některé z mimoevropských destinací. Důvod k tomuto exportnímu triku není žádným tajemstvím – za dovoz dílů se platí menší clo.
Račte dál
BMW nedrží pod pokličkou ani to, jak své motocykly šroubuje dohromady. Chcete-li kouknout technikům u výrobní linky přes rameno, stačí si zarezervovat termín prohlídky a vyrazit – podobně jako my – směr Berlín. Exkurze trvá zhruba dvě hodiny, takže ji stihnete i s cestou tam a zpátky v pohodě za jeden den. Průvodce vám na uvítanou řekne pár zajímavých slov o historii a současnosti, odrecituje povinné bezpečnostní instrukce, rozdá sluchátka a pak už se vyráží ve skupině do provozu.
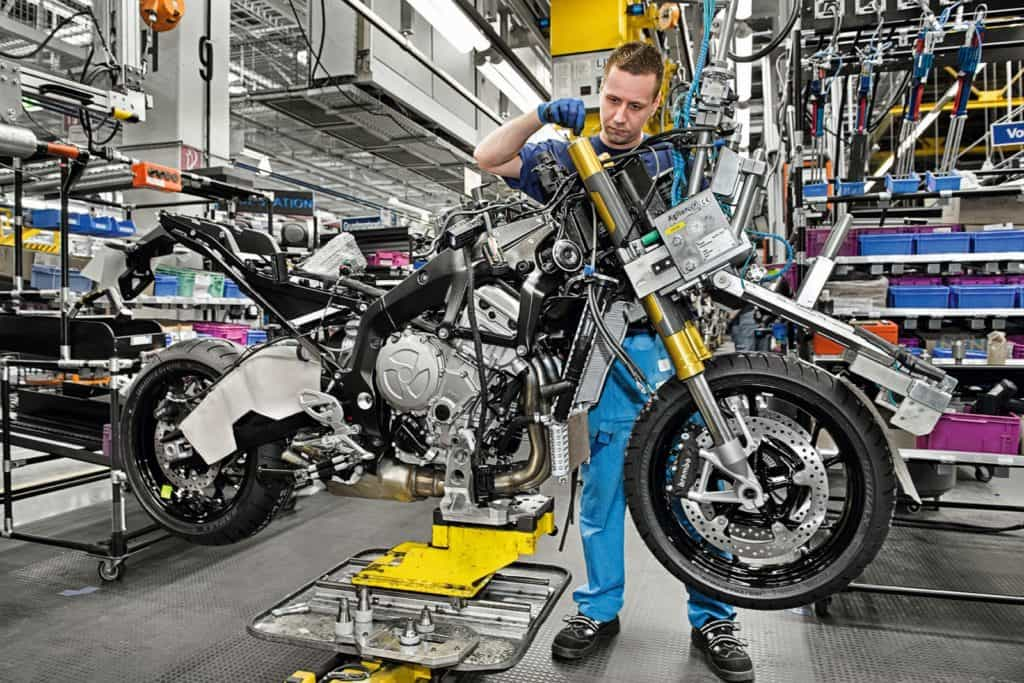
Prohlídka je uspořádaná pěkně chronologicky, a to nejen z hlediska postupu výroby. Začíná se v původní hale, kde se kdysi dávno vyráběly letecké motory. Ta dnes funguje jako přípravna součástek pro boxery, řadové dvou-, čtyř- i šestiválce. Z hrubých odlitků tu vznikají kartery (kromě těch pro největší šestiválce, které se kvůli své šířce obrábí na větších strojích v Mnichově), klikové hřídele, ojnice a to všechno za přepečlivé a několikanásobné kontroly. Na jednom automatu se testují a vyvažují rotující součástky, vedle jiný robot třídí ojnice do sad tak, aby spolu v jednom motoru běhaly ty s nejpodobnější hmotností. Všechno přitom běží v poklidném, leč vytrvalém tempu, ale hlavně na každém kroku je vidět německý smysl pro pořádek. I v tomto relativně špinavém provozu je všechno jako ze škatulky, a vůbec to nepůsobí strojeným dojmem, jako když doma vyluxujete jen kvůli návštěvě.
Ještě větší „ordnunk“ panuje ve vedlejší montovně motorů, pro kterou už Němci museli postavit moderní budovu. A přestože se skládání přesných součástek do sebe neobejde bez lidských rukou, při většině úkonů tu opět pomáhá technika. Počítače (respektive osobní čipové karty) znají dokonce i tělesnou výšku každého zaměstnance a podle ní mu po příchodu ke stroji nastaví co nejpohodlnější polohu pro jeho ovládání.
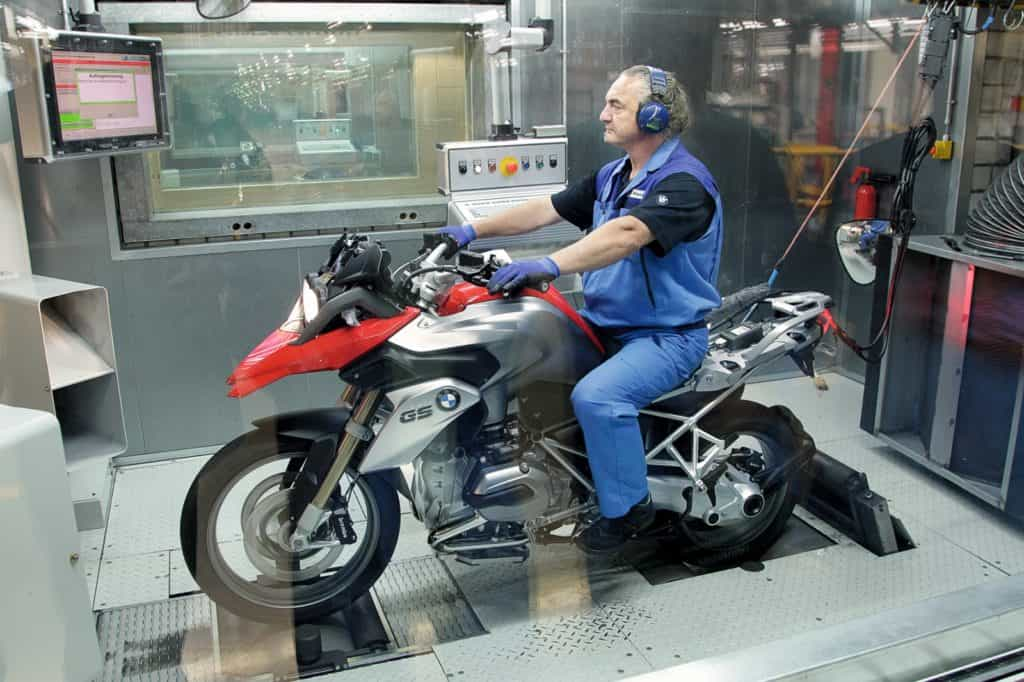
Na pohodu při práci se tu vůbec hodně dbá – v odpočinkovém koutě uvidíte stolní fotbálky, boxovací pytle či lehátka. No kdo by nechtěl dělat ve firmě s takovým zázemím? Technik v montovně přitom není vystaven žádnému velkému stresu, protože každý následující pracovní krok vidí před sebou na monitoru a v podstatě nemá šanci udělat chybu, ani když se zaposlouchá do přímého přenosu z finále fotbalového mistrovství světa.
Ani s hledáním těch správných součástek si nemusí lámat hlavu – všechny, které potřebuje pro daný úkon, dostane od kolegů ze „supermarketu“ přesně vyskládané v platu z tvrdé pěny. Trochu to připomíná chirurgické nástroje vyrovnané na stolku před operací. Do jednoho motoru postupně přijde až 600 dílů a kompletní montáž trvá zhruba dvě hodiny. Pak následuje kontrola těsnosti a „studený“ test, při kterém se poprvé protočí klika v ložiscích. K benzinu si však motor přičichne až během závěrečné zkoušky zkompletovaného motocyklu na brzdě.
Na německé svatbě
Svařovna a lakovna nejsou z bezpečnostních důvodů návštěvám zpřístupněné, a tak prohlídka pokračuje rovnou u linky, kde se potkávají motory s rámy a dalšími komponenty. Každá motorka absolvuje svou pouť na pohyblivém závěsu, který postupně projede oběma patry haly, propojenými výtahy. Montážních linek je tu několik, ale každá je schopná vyrábět prakticky libovolný model. Nejedou se zde dokonce ani žádné obří série – ve frontě za sebou můžete vidět pět R 1250 GS (a každé z nich navíc v jiné výbavě) následovaných čtyřmi S 1000 R a za nimi třeba dvě „ertéčka“. Jenom elektrické skútry se skládají na zvláštní lince, kvůli odlišným nárokům na vybavení a kvalifikaci techniků.
Montéři bavoráků s klasickými motory jsou po zaškolení schopni obsluhovat minimálně pět stanovišť, ti nejlepší se postupně naučí všechny pracovní úkony a mohou pak zaskočit za kolegu na jakémkoli postu. Ne že by se snad kola výroby nesměla ani na vteřinu zastavit – stres při práci je tu skutečně tabu –, ale když se má v sezonní špičce stihnout sešroubovat osm set kusů za den, nejsou prostoje zrovna vítané. Jedinými nezastupitelnými členy týmu jsou testovací jezdci, kterým projdou rukama všechny vyrobené motocykly. Ti během ostré zkoušky na brzdě překontrolují všechny funkce – od quickshifteru až po klakson – a pak už se nad motorkou může zaklapnout víko přepravního boxu.